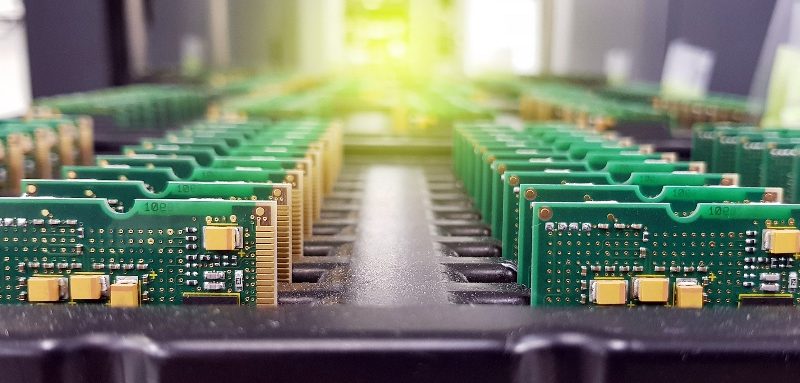
When we think of how our electronic devices operate, we often overlook the complex processes that make them function. One such vital process is PCBA, or Printed Circuit Board Assembly. Whether it’s smartphones, computers, or medical devices, it plays a fundamental role in bringing electronics to life. This article will explore what PCBA entails, how it’s made, the challenges faced during production, and its applications across various industries.
What is PCBA? A Comprehensive Overview
PCBA stands for Printed Circuit Board Assembly, which is the process of assembling electronic components onto a bare Printed Circuit Board (PCB) to create a functional unit. While the PCB provides the structural foundation with a network of conductive pathways, it is the PCBA process that transforms it into a working circuit capable of driving electronic functions.
The PCBA Manufacturing Process Explained
PCBA involves several critical steps, each with its purpose and technical challenges. Here’s an in-depth look at the process:
Step 1: Solder Paste Application
- Process: The first step involves applying solder paste, a mixture of powdered solder and flux, to the board’s pads. This is done using a stencil and a squeegee, ensuring precise application only to areas where components will be mounted.
- Importance: The solder paste acts as the adhesive that secures the components to the board before permanent soldering.
Step 2: Component Placement (Pick and Place)
- Automation: Modern PCBA production uses high-speed pick-and-place machines to accurately position components on the board. These machines can place components as small as 01005 (0.4 mm × 0.2 mm) and handle various shapes and sizes.
- Precision: Component placement is crucial for maintaining electrical connectivity and circuit function.
Step 3: Reflow Soldering
- Process: Once the components are placed, the board goes through a reflow oven. The controlled heat melts the solder paste, forming secure connections between the components and the PCB.
- Technical Considerations: Reflow soldering must be carefully controlled to prevent overheating, which could damage sensitive components or lead to solder defects like cold joints and bridges.
Step 4: Inspection and Quality Control
- Automated Optical Inspection (AOI): This non-contact method checks for defects such as misplaced, skewed, or missing components. High-resolution cameras scan the board and compare it against a pre-loaded reference.
- X-ray Inspection: For complex boards with Ball Grid Array (BGA) components, X-ray inspection is used to identify issues hidden beneath the component’s surface.
- Functional Testing: In-Circuit Testing (ICT) and Functional Circuit Testing (FCT) verify the board’s electrical performance and behavior under real-world conditions.
Common Challenges in PCBA Manufacturing
Despite advances in technology, PCBA production comes with its own set of challenges:
- Miniaturization: The ongoing trend toward smaller, more compact devices means components are getting smaller and more densely packed. This increases the complexity of placement and inspection.
- Thermal Management: Maintaining appropriate temperatures during reflow soldering is critical, especially when using lead-free solder with higher melting points.
- Double-Sided Assembly: Many modern PCBs have components on both sides, requiring careful handling and additional reflow cycles, increasing the risk of heat damage and misalignment.
- Material Quality: Ensuring the quality of PCBs and components is essential to avoid production defects and ensure product reliability.
Types of PCBA: Surface-Mount Technology (SMT) vs. Through-Hole Technology (THT)
There are two main types of PCBA based on component mounting:
- Surface-Mount Technology (SMT): Components are mounted directly onto the PCB’s surface using solder paste and reflow soldering. SMT allows for smaller, high-density assemblies and is the most common type of PCBA used today.
- Through-Hole Technology (THT): Components have leads that pass through holes in the PCB and are soldered on the opposite side. While THT provides strong mechanical bonds, it is often reserved for larger or more robust components in applications where reliability under stress is critical.
The Role of PCBA in Various Industries
- Consumer Electronics: Devices like smartphones, tablets, and laptops depend on PCBA for their intricate functions. The demand for compact, multifunctional gadgets drives innovation in high-density PCBA.
- Automotive Electronics: Modern vehicles are equipped with complex electronic systems, such as Advanced Driver-Assistance Systems (ADAS), infotainment, and engine control units (ECUs). The reliability and durability of PCBA are paramount in these safety-critical applications.
- Medical Devices: PCBA must meet stringent quality and reliability standards in medical devices. Applications range from diagnostic tools to life-support systems, where failure is not an option.
- Aerospace and Defense: In these fields, PCBAs must endure harsh environments, including extreme temperatures, vibrations, and radiation. High-reliability PCBA ensures that systems operate flawlessly in critical missions.
- Industrial Automation: Factories and plants rely on PCBA for controlling automated processes, robotics, and sensors.
Future Trends in PCBA Manufacturing
As technology evolves, so does the landscape of PCBA manufacturing. Here are some emerging trends:
- Advanced Manufacturing Techniques: 3D printing and additive manufacturing are being explored for rapid prototyping and custom PCBAs.
- Machine Learning and AI: The incorporation of AI in quality inspection and process optimization is improving the speed and accuracy of defect detection.
- Flexible PCBs: The rise of wearable technology and flexible devices is driving the development of flexible PCBs and new PCBA techniques to accommodate non-traditional shapes and materials.
- Sustainability Initiatives: Eco-friendly manufacturing practices, such as using lead-free solder and reducing e-waste, are becoming standard.
Conclusion: The Importance of PCBA
PCBA is the backbone of modern electronics manufacturing, transforming PCBs into functional units capable of supporting a vast range of applications. Whether powering a simple gadget or a complex industrial machine, the quality of PCBA directly impacts the performance, durability, and reliability of electronic products. As new technologies emerge, the PCBA process will continue to evolve, meeting the growing demand for faster, smaller, and more efficient electronics.
Understanding the intricacies of PCBA helps appreciate the effort behind every device we use, highlighting the significance of precision engineering and continuous innovation in the field.